Cast Iron vs Mild Steel Welding Tables
Cast Iron vs Mild Steel Welding Tables: How to choose?
Choosing a welding table isn’t just about buying a surface to work on—it’s about investing in your workshop’s efficiency and precision. With using welding tables our clients have doubled the production and reduced their costing for fixtures by using modular fixtures.
Mild steel and cast iron are two common materials for these tables. To assist you in selecting the one that best suits your needs, this article deconstructs their salient characteristics.
Material Properties: Mild Steel vs. Cast Iron
-
Cast Iron:
Known for its remarkable stability, this material provides excellent rigidity and resistance to vibration. Because of this, it is perfect for precision work settings where even a small amount of movement or warping might result in mistakes. - Mild Steel: Mild steel welding tables are a popular choice for ordinary fabrication work since they are lighter and more adaptable. It is a reliable material for many workshops, especially those that specialize in medium-duty work, even if it is not as rigid as cast iron.
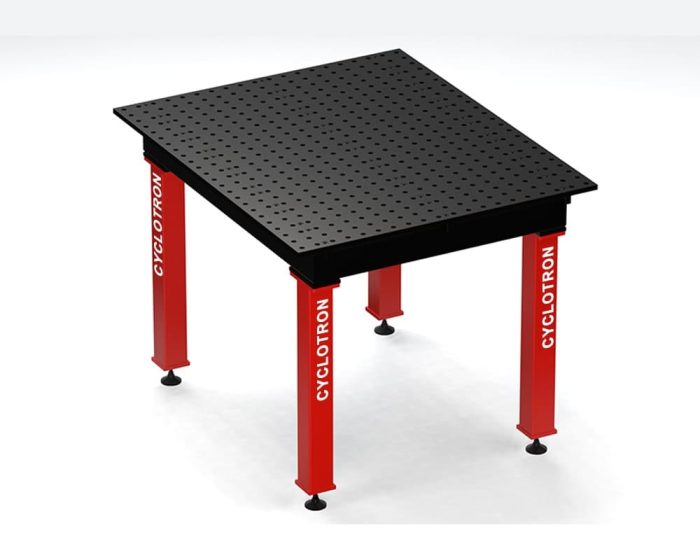
Difference between Cast Iron and MS Welding tables.
Precision and Flatness Stability
– Cast Iron: It’s flatness can go upto 0.1mm per metre for cyclotron welding tables
– Mild Steel: The flatness can be upto 0.3 mm per meter for cyclotron welding tables
Load-Bearing Strength
– Cast Iron: Supports exceptionally heavy loads, making it a favorite in heavy industry. Load bearing strength of mild steel welding table is upto 1000 kgs/sq meter
– Mild Steel: Suitable for moderate loads, which covers most general workshop needs. Load bearing strength of mild steel welding table is upto 600 kgs/sq meter
Resistance to Heat
– Cast Iron: Withstands heat and surface wear from welding activities effectively.
– Mild Steel: May require coatings or periodic maintenance to prevent surface degradation. Nitriding is the heat treatment offered on the Cyclotron welding table to overcome this
Longevity and Maintenance Needs
– Cast Iron: Minimal upkeep, with a long service life and excellent durability
– Mild Steel: May demand more frequent maintenance, especially under demanding conditions.
Common Applications of both the welding tables
- Cast Iron Welding Tables: - Automotive and aerospace applications - Environments requiring strict precision - Heavy-duty fabrication
- Mild Steel Welding Tables - Prototyping and medium-scale projects - Workshops prioritizing cost-efficiency - Small to medium manufacturing setups
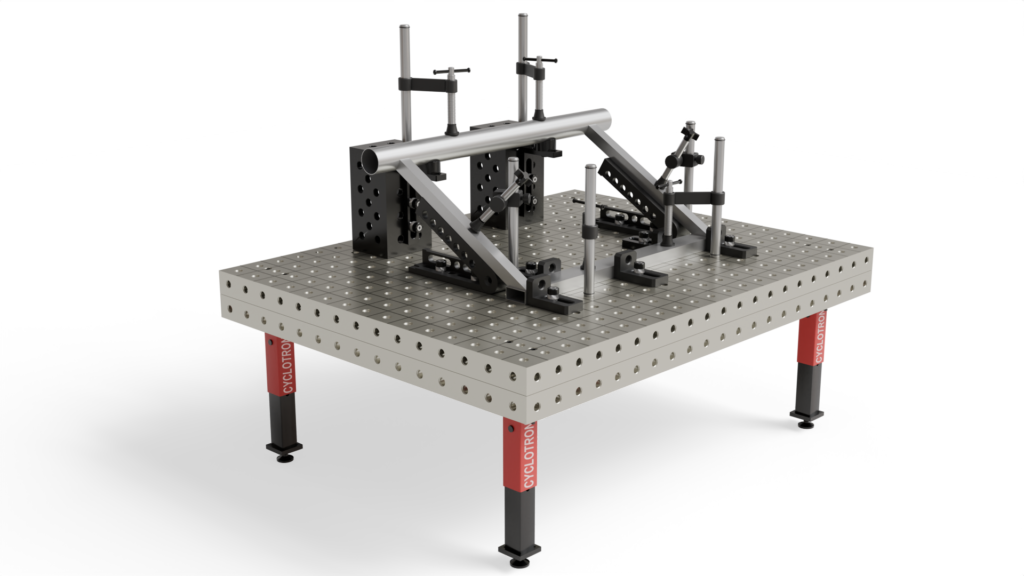
Cost Factors to Keep in Mind
Cast Iron: The higher upfront investment often pays off with durability and consistent performance in demanding settings
Mild Steel: More affordable initially but may incur maintenance expenses over time, especially if exposed to heavy loads, otherwise this one is ideal for load upto 600 kgs per meter square
Tips for Selecting the Right Welding Table
- Evaluate Precision Requirements: Are you working on high-accuracy projects, or do general tolerances suffice?
- Analyze Load Capacity Needs: Consider the typical weight and size of your components.
- Factor in Budget: Weigh upfront costs against potential maintenance expenses.
- Consider Tool Compatibility: Ensure compatibility with your existing clamping systems.
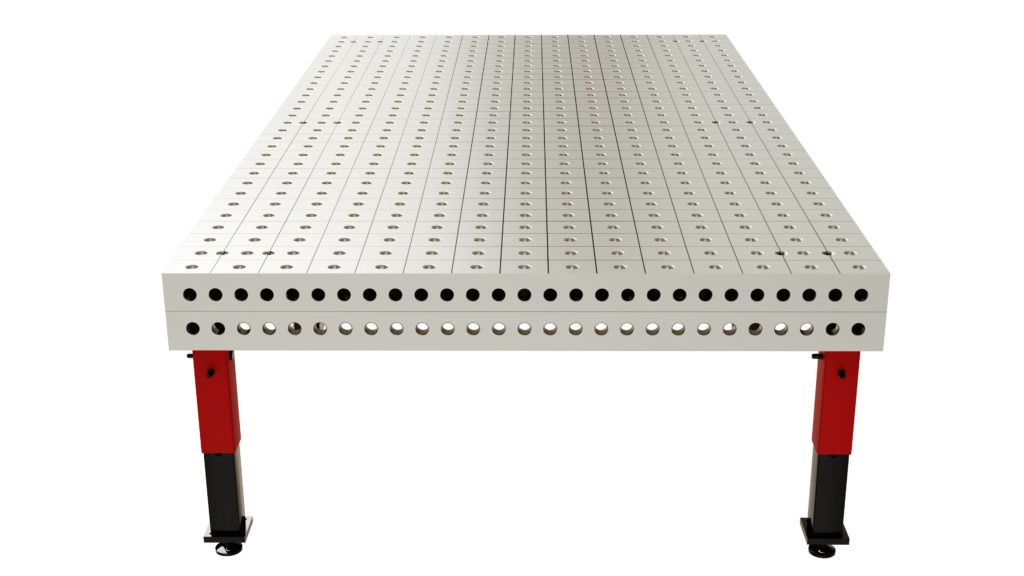
Final Recommendation by Cyclotron
If your operations demand top precision and heavy load-bearing capacity, cast iron is a dependable option. For more versatile or cost-conscious setups, mild steel delivers a solid balance between function and affordability.
How to choose a suitable welding table?
There are plenty of things while considering a suitable fixture table for YOU. It could start from what should be the size? Should it be 3D, 2D, Rotary, or slotted table? What should be the thickness?
Benefits of Rotary welding table
The use of rotary welding tables in the manufacturing industry has drastically increased due to the increase in production rate, better welding quality, greater Business ROI, and many more.
Types of Welding tables
Most of the welders perform all the fabrication work on the floor. One can work on the shop floor without a welding table. No grounding needed, no worry about cutting the base etc.