Robotic Welding Fixtures
Robotic welding fixtures
Robotic welding fixtures are work holding systems specifically engineered to position parts consistently while performing automated welding operations.
We at Cyclotron engineer and produce high-performance robotic welding fixtures that provide repeatable alignment, accommodate high-speed automation, and remove manual positioning discrepancies.
Our modular fixtures are designed specifically to accommodate both the geometry of your workpieces and the dimensions of your robotic welding cell, allowing consistent weld quality and improved throughput
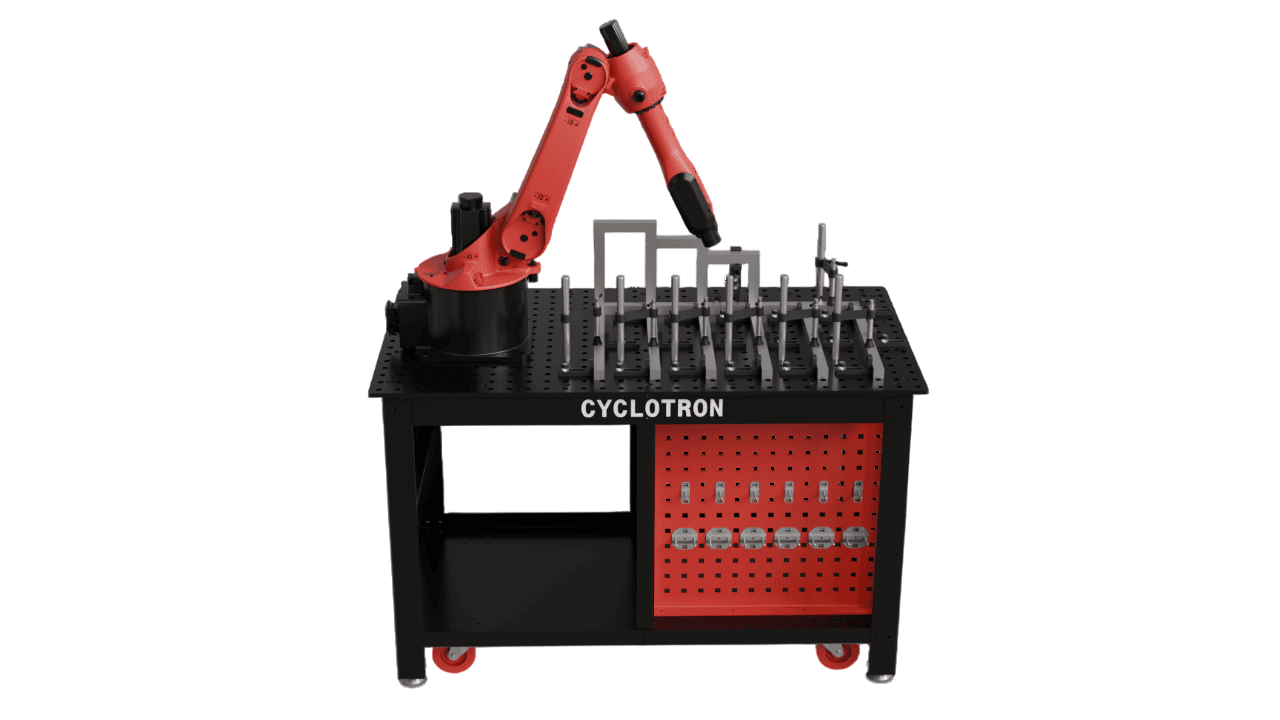
Benefits of Robotic welding fixtures
-
Key Benefits
Repeatability: Consistent positioning of the part during each cycle improving weld accuracy.
Cycle Time Reduction: Helpful for quick loading and unloading thereby reducing non welding time.
Enhanced Quality: It reduces welding distortion as well as improves weld time.
Customization: Fixtures are tailored to your part which thereby can be changed once your part is changed
Durability: Built with hard quality materials to withstand heat, spatter, and mechanical stress.
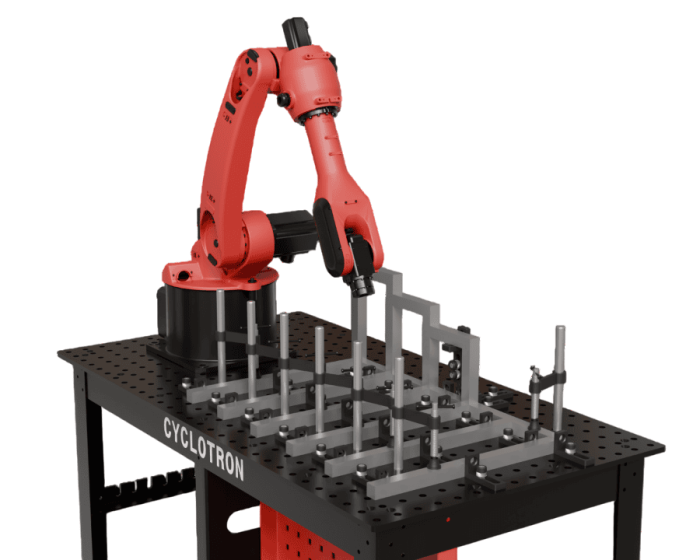
Robotic welding fixture design
Cyclotron’s robotic welding fixtures design is built with industrial requirements in mind:
Construction: Heavy-duty mild steel or aluminum base frames with support ribs
Clamping Options: Manual, pneumatic, or hydraulic clamps based on cycle and part complexity
- Datum Control: Fixed locating pins and adjustable supports for maintaining tolerances
Modularity: Modular elements for easy changeover in multi-part setups
Sensor Integration: Provisions for part-present sensors and verification systems
Weld-Resistant Materials: Fixtures coated or treated to resist weld spatter and heat buildup
Robot-Friendly Layout: Designed to optimize access angles for robotic arms
Robotic welding on Cyclotron welding table
Cyclotron’s welding tables are suitable for robotic welding and cobot welding processes. The clamps allows the robot to welding accurately holding the product tightly such that it does not move while welding.
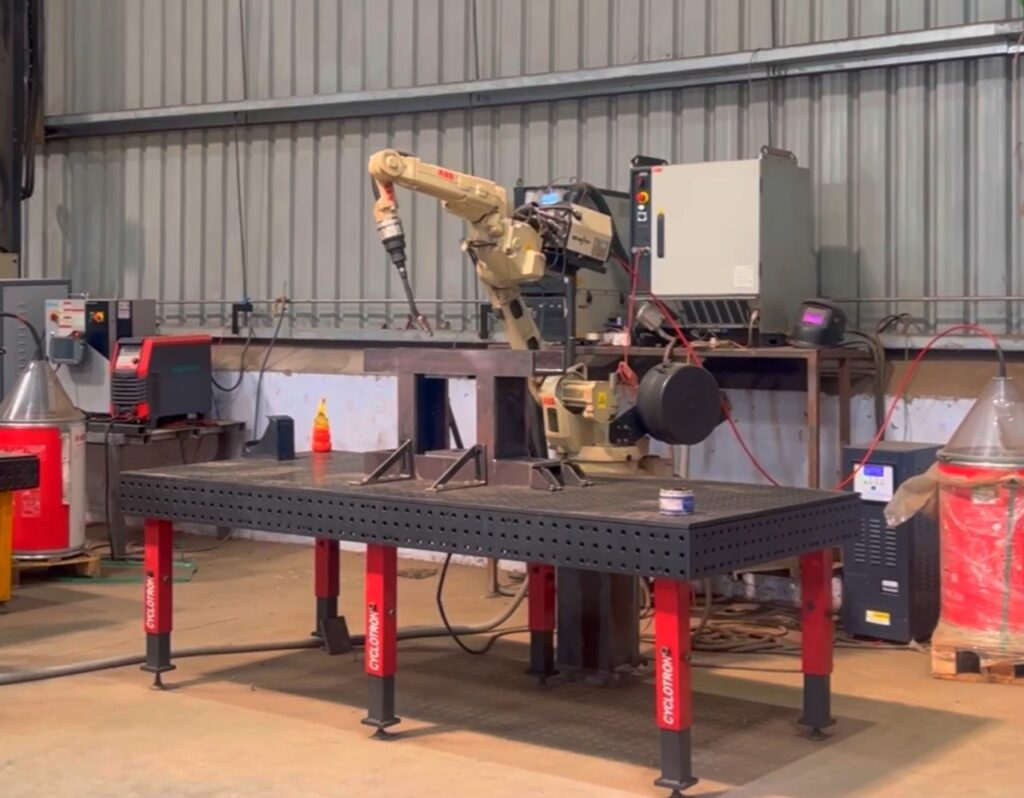
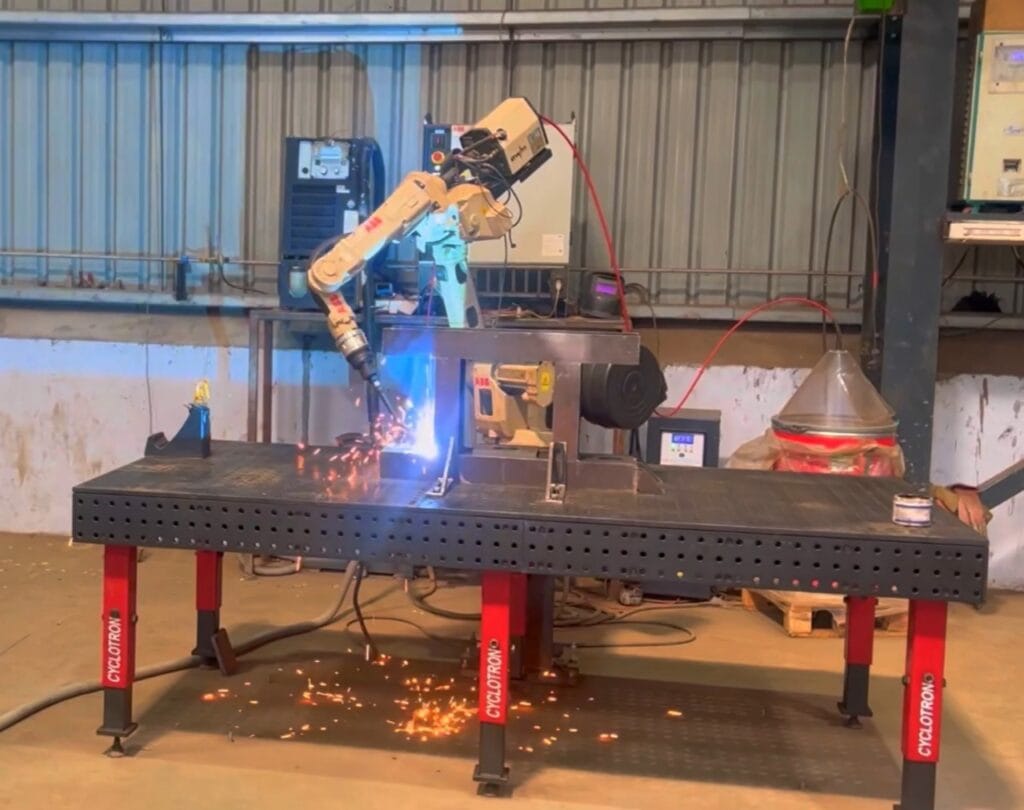
Welding Fixture Development Process
-
Requirement Collection – Share your part drawings, welding parts, and production targets
Design Phase – We prepare 3D models of fixture concepts and finalize with your team
Manufacturing – Fixtures are machined, assembled, and inspected at our facility
Validation – Dry runs and weld simulations to ensure functionality
Delivery & Support – Shipped with installation guidance and optional robot path tuning support
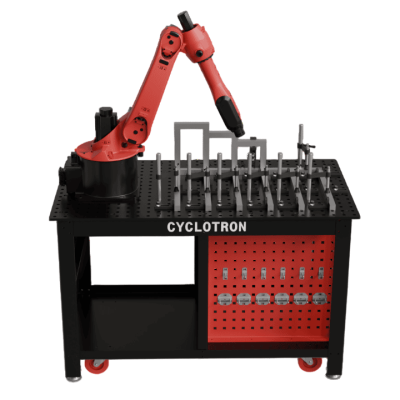
FAQS
Q: Can Cyclotron fixtures be used with any robot brand?
Yes. Our fixtures are compatible with all major industrial robot systems including ABB, Fanuc, Yaskawa, KUKA, and Panasonic.
Q: Do you provide only the fixture or complete turnkey welding cells?
Primarily, we design and supply robotic welding fixtures. However, if needed, we can collaborate with robotic integrators for turnkey solutions.
Q: What’s the typical lead time?
Lead time depends on complexity but typically ranges from 3 to 6 weeks after design approval.
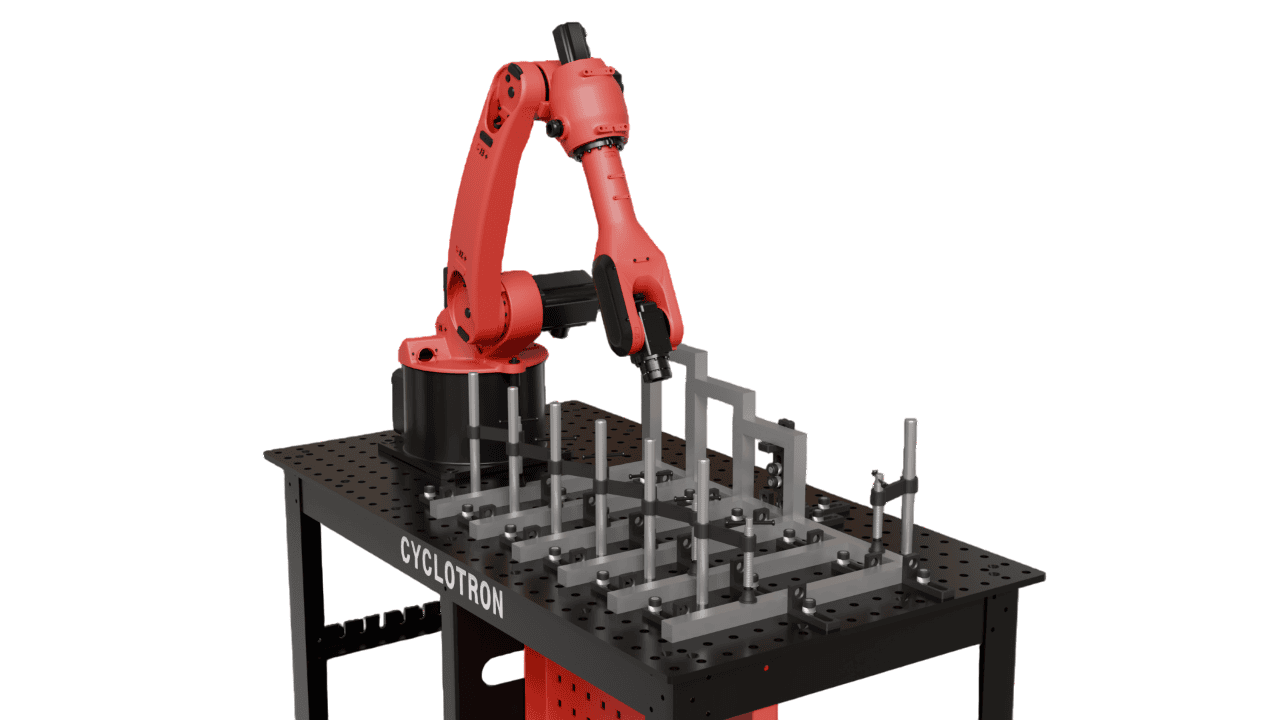
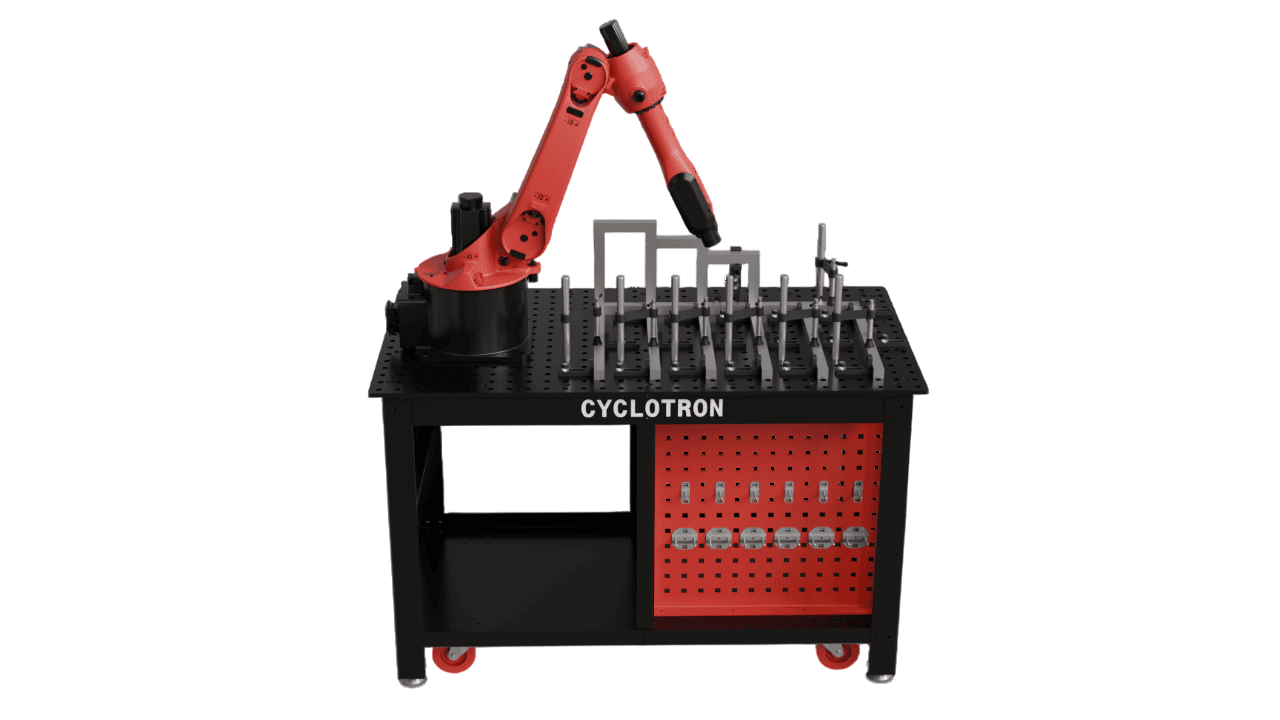
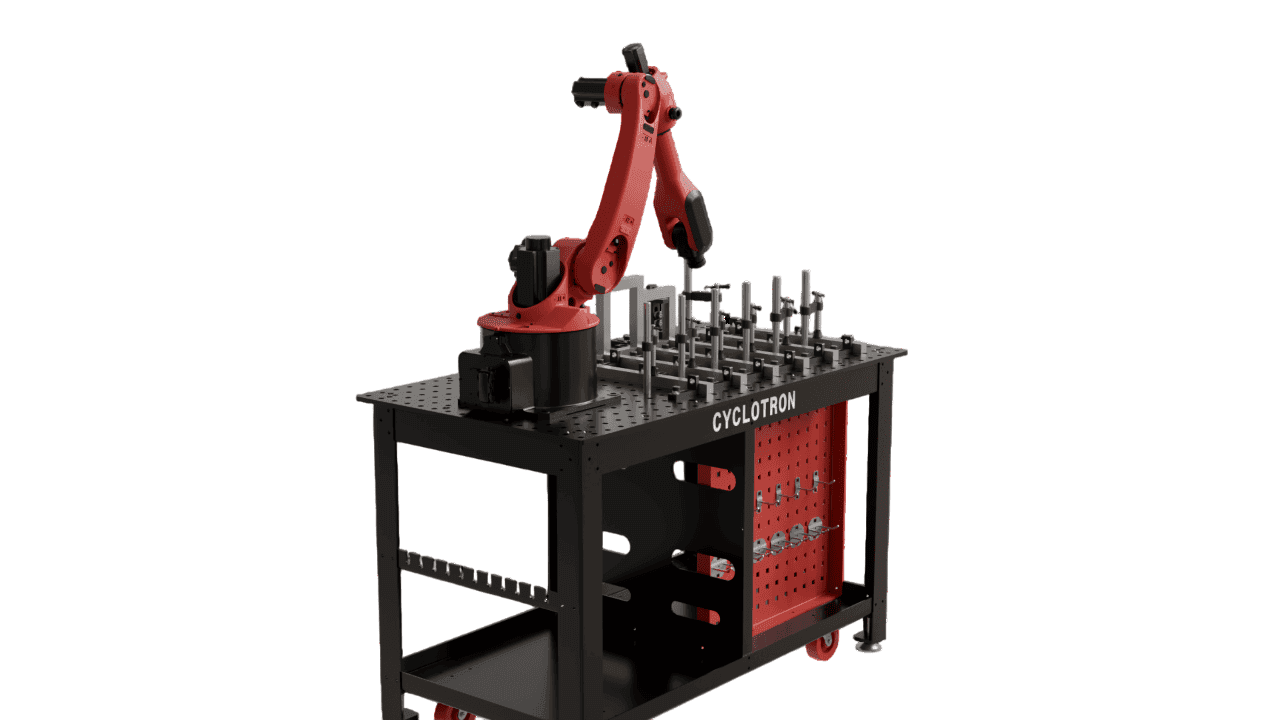

Our Products
Coming soon..
How to choose a suitable welding table?
There are plenty of things while considering a suitable fixture table for YOU. It could start from what should be the size? Should it be 3D, 2D, Rotary, or slotted table? What should be the thickness?
Benefits of Rotary welding table
The use of rotary welding tables in the manufacturing industry has drastically increased due to the increase in production rate, better welding quality, greater Business ROI, and many more.
Types of Welding tables
Most of the welders perform all the fabrication work on the floor. One can work on the shop floor without a welding table. No grounding needed, no worry about cutting the base etc.